Australia first IR Technology, more comfort inside without giving up natural light
We are the official distributor in Australia for dott.gallina polycarbonate roofing and systems featuring new infrared IR Technology. The protective IR ray filter range provides innovative solutions for building applications where adequate natural lighting is desired whilst reducing heating to the inside. This results in energy savings for cooling (reduces the temperature increase by up to 25%) and lighting (increases the light transmission by up to 60%). The roof sheeting is available in a range of thicknesses and dimensions and have many applications including skylights, tunnels, greenhouses and gazebos.
Comparison of dott.gallina’s IR technology with other products
There are similar products on the market, but this new technology permits the production of products with the filter of protection against infrared only on the external surface, to avoid the complex heating of the elements and consequent transmission of the heating to the inside.
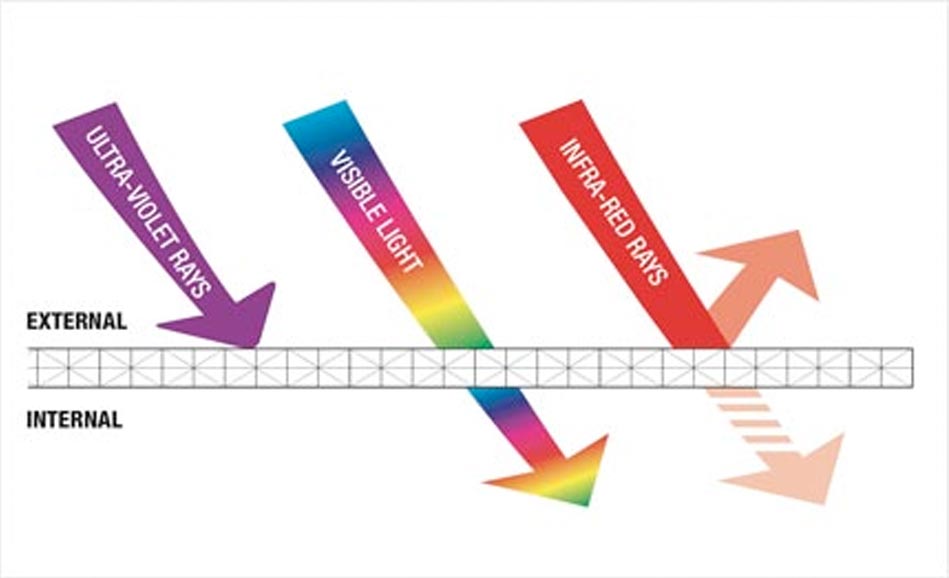
Internal temperature reduction comparison
We are the official distributor in Australia for dott.gallina polycarbonate sheets and systems (as made by Arco Plus) featuring new infrared IR Technology. The protective IR ray filter range provides innovative solutions for building applications where adequate natural lighting is desired whilst reducing heating to the inside.
Bi-Colour 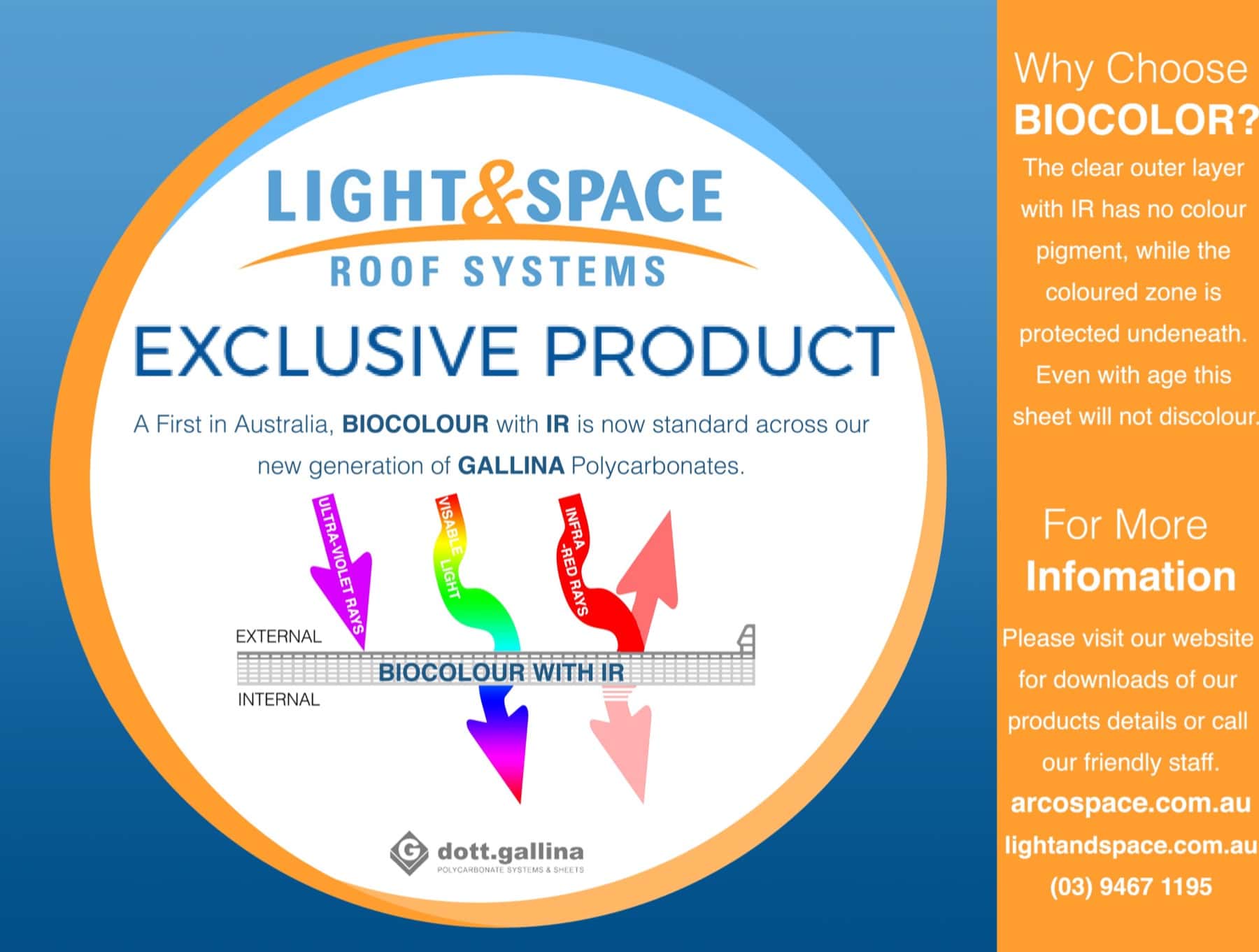
The technology of double colour.
The arcoPlus panels can be produced also with different colours on the two sides, this is due to the extrusion of two different masses, one for the inner surface and another for the external one.
The particular productions technology allows to manage simultaneously the light transmission and colour effect, maximizing the projects visual impact.
Rafter System 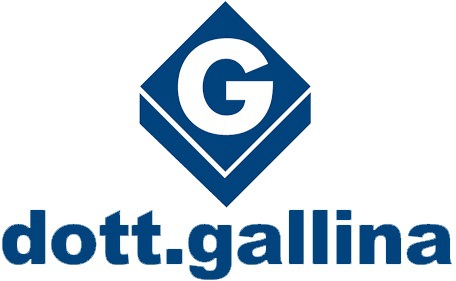
All of our structures utilise our in-house designed and engineered AB free span rafter system. It locks polycarbonate roofing together without any screws and allows for thermal movement, which eliminates expansion noise.
The lightweight AB rafters that we use can span up to 6m in a curved design or 5m in a flat-pitched one. Larger spans of up to 9m can be achieved if required through the use of a larger bar.
Other posts, beams and brackets are comprised of Duragal steel and all metal components are powdercoated to achieve an attractive and durable finish. All fixings are concealed to maintain this smooth, clean finish.
We own the patent for building Glazed structures. View our patent certificate here.
All roof sheeting panels used in our products are made by dott.gallina.
arcoPlus ®
547 | 549 | 684/6104/6124 | 626 | 9207/9257/9327 | DBconnect | 5613 | |
---|---|---|---|---|---|---|---|
Materials (1.) | PC – Polycarbonat | ||||||
Cover width [mm] | 500 | 500 | 600 | 600 | 900 | 600/900 | 500 |
Dimensions [mm] | 524×40 | 524×40 | 600×8/10/12 | 600×20 | 900x 20/25/32 | 600/900×90/114 | 535×60 |
Surface protection with UV protection- Coextrusion (1B.) |
One-sided | One-sided | Single-sided Double-sided Reversò | Single-sided Double-sided Reversò | Single-sided Double-sided Reversò | One-sided or two-sided | One-sided |
Thermal transmittance coefficient [W/m2K] (2.) |
1.1 | 1.0 | 3.0/ 2.7/ 2.5 | 1.7 | 1.7/ 1.4/ 1.3 | 0.51 – 0.84 | 0.75 |
Sound insulation index [dB] ISO 717-1 |
21 | 21 | 18/ 18/ 19 | 20 | 20/ 20/ 21 | 26 | 22 |
Expansion coefficient [mm/m°C] |
0.065 | ||||||
Temperature resistance [°C] (3.) |
– 40 to +120° | ||||||
Delivery lengths [m] | Unlimited | ||||||
Standard delivery colours (4.) | crystal, opal, green, bronze | crystal, opal | crystal, opal, blue, bronze | crystal, opal | crystal, opal | crystal, opal | |
Light transmission depending on the color [%] |
31-60 | 28-50 | 36-70 | 33-58 | 41-55 | 11-39 | 37-20 |
Transmission of UV radiation |
0 – 5% | ||||||
Fire behaviour (5.) | B – s1, d0 | ||||||
Hail impact test (7.) | + | ||||||
Quality control (8.) | + | ||||||
Building approval (9.) |
+ | + | |||||
CE classification | + | + | + | + | + | + | + |
* estimated values without test certificate
** other transparent or opaque colours on request
Legend
1. Raw material
Proculit light panels are made from:
- Tin-stabilized, plasticizer-free, highly impact-modified polyvinyl chloride (PVC), with additional “longlife” coextrusion for outstanding UV radiation and weather resistance or from
- Extremely impact-resistant, weather-resistant polycarbonate (PC) with “longlife” coextrusion
Material properties:
Condensation: Polycarbonate is a hygroscopic material that allows water vapor to diffuse through the material. Depending on the humidity level and the temperature inside and outside the building, condensation can usually occur temporarily in the chambers. However, this does not affect the quality, function or service life of the glazing and does not constitute a defect/reason for complaint.
Glazing panels made of PVC and especially polycarbonate are not compatible with certain chemical agents (information on chemical compatibility available on request). In particular, contact with aqueous solutions of cooling lubricant oils can lead to stress cracks (special coatings against stress cracks available on request).
2. Insulation behaviour
The U-values are measured in accordance with DIN ISO 6946 in W/m²K for horizontal heat flow. Up values refer to the light panels, Uf to the frame profiles. A combination of light panels with thermally separated aluminum profiles generally meets the requirements of EnEV 2009.
3. Thermal stress and chemical resistance
- The upper operating temperature of Prokulit light panels made of PVC must not exceed 55° C.
- Do not install in a closed area without ventilation (particularly in the roof area as a false ceiling or insulation). Avoid heat build-up at all costs.
- Paint bars, plates and reinforcements in direct contact with the panels white. Avoid contact with fresh wood impregnations.
Protection against contamination
If the system is susceptible to contamination (e.g. dust, high insect infestation from the inside), we recommend sealing the open chambers at the top and bottom with adhesive tape, which may in individual cases lead to a higher proportion of temporary condensation in the chambers. A secure seal can be achieved with a butyl tape. If there is smoke and welding fumes inside the building, the suction anchor groove in the area of the base and frame profiles should also be sealed from the inside. Make sure that the adhesive is not damaged by screw heads when pushing in/lowering. We therefore recommend mounting the frames with countersunk screws.
4. Delivery colours – Project Caleido
Standard colors as per table, translucent or solid special colors on request.
Examples:
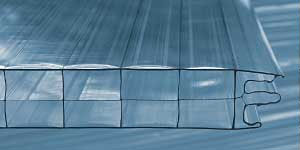
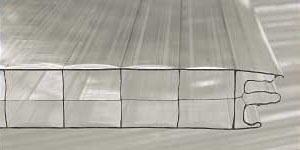
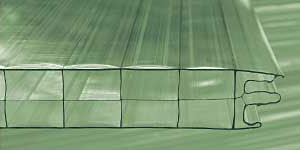
Caleido System
The Caleido project offers coloring of the glazing panels far beyond the known color palette for unlimited color design. The desired color can be taken from samples and translated into the corresponding polycarbonate masses for production. Both translucent colors and opaque colors are available.
5. Light and radiation transmission
Depending on the number of shells and the colors of the light panels, the light transmission varies from 60% to almost 0%. The total energy transmission = g-value as a measure of the energy input to the inside correlates closely with the values for the light transmission. The transmission of UV radiation is almost 0%. The transmission of high-energy IR radiation can be reduced disproportionately to the light transmission by means of a “Heatbloc” coextrusion. The most effective protection against excessive heating of the building is provided by opal coloring.
Polycarbonate panels reflect only a very small proportion of radar radiation and are therefore particularly suitable for buildings near airports, as the surveillance radar is not interfered with.
6. Fire behaviour
PC 540-3/ PC 540-6, PC 540-7: B 2 non-flaming dripping, in accordance with DIN EN 1350-1-1- B S1 dO flame retardant, non-flaming dripping, Swiss fire index number 5.1. (Safety Institute) B1, easily meltable (collapsing) roof and wall surfaces for heat extraction at temperatures < 300°C, ignition temperature approx. 450°C,
PC 560-11: B 2 non-flaming dripping, B S1 d0 according to DIN EN 1350-1-1 flame retardant, non-flaming dripping, easily meltable (collapsing) roof and wall surfaces for heat extraction at temperatures <300°C, ignition temperature approx. 450°C,
ArcoPlus 625, 547,549, Series 600 Reverso, Series 900 Reverso: flame-retardant in accordance with DIN EN 1350-1-1 B S1 d0, non-burning, dripping, easily melting (collapsing) roof and wall surfaces for heat extraction at temperatures <300°C, ignition temperature approx. 450°C
7. Ball throwing safety
According to DIN 18032, Part 3,
without restriction (puck-proof), by the Research and Materials Testing Office
of Baden-Württemberg. (46/20964), except hockey ball for PVC.
8. Hail impact test
according to SIA 280 according to test specification 2009 VKF HW5 No. 8, for new goods up to class 5
9. Certification and third-party monitoring
Self-monitoring through laboratory and pilot plant tests
10. General building approval
by the German Institute for Building Technology in Berlin with regard to structural safety
(Ü-sign for PC: Z-10.1-328, for PC 560-10: Z-10.1-477)
11. CE classification according to EN 14963: 2006
12. Fall-through safety
According to GS-Bau18 (2001) and impact resistance according to SB350ETAG-010
(Report 90/07.1GD)
Fall protection according to ETB – Directive (06/1985)
FAQ
General
What is polycarbonate?
The term Polycarbonate describes a polymer which is composed of many (“poly”) identical units of bisphenol A connected by carbonate-linkages in its backbone chain. Chemically, a carbonate group is a di-ester of carbonic acid, the result of which is a polymeric chain. Polycarbonate is transformed into the required shape by melting it and forcing it under pressure into a mould or die. There are two dominant processes involved in making products from polycarbonate:
Extrusion : The polymer melt is continuously pressed through an orifice called a “die”, which gives the molten polymer its final shape. This process makes it possible to create infinitely long pipes, profiles or sheets.
What thickness should I use?
Does polycarbonate yellow?
Gallina’s PoliCarb® and arcoPlus® products are all UV-coated on at least one side to prevent the sun’s harmful UV rays from damaging or discoloring our polycarbonate sheets and panels. See our 10 year warranty for more details.
Can Gallina’s multiwall polycarbonate panels be used for radius applications?
One of the unique characteristics of polycarbonate that makes it a preferred material over glass is that it can be cold bent for arched applications. Panel thickness and structure design will impact the extent of radius bending. Click here to go to the bending capabilities.
What do I clean Gallina’s PoliCarb® and arcoPlus® panels with?
GALLINA panels should be protected from abrasion by the installer. After installation, panels should be washed with mild soap or detergent and lukewarm water using only a clean sponge or soft cloth, then rinsed with clean water. Fresh paint, grease, and smeared glazing compounds maybe removed before drying by rubbing lightly with a good grade of naphtha or isopropyl alcohol followed by a final wash with mild soap or detergent and final rinse.
What do I use to cut Gallina’s Policarb® and arcoPlus® panels?
Use a circular saw with plywood blade or jig saw with fine tooth blade. This produces clean, even cut. Cut sheet before taking off film, or static charge will attract fine chips to channels. Remove any fine shavings or chips prior to installation. Condensation moving through layers continues cleaning channels, but get clean as possible. Leave film on sheet until ready to install, remove in an area free from dust. Thinner sheets may be cut with a utility knife using a clamp and secured straight edge to ensure an accurate, straight cut.
Can I use polycarbonate on an angled or straight roof?
It is recommended that polycarbonate be used on slopes no less than 5 degrees.
Will Gallina Australia work with me on drawings and make recommendations?
Yes, Gallina has a trained staff and resident architect available to work with you and your plans to make recommendations for all your polycarbonate building needs. We are also supported by our other manufacturing facilities and their staffs to ensure that all your questions are answered.
Technical
Does condensation affect the performance of polycarbonate sheet?
In common with many glazing materials polycarbonate sheets can develop condensation as a result of environmental factors. It does not affect the performance of solid or multiwall polycarbonate sheets; the effects are purely visual and normally temporary. At all stages of the handling, transporting and installation of multiwall sheets care should be taken to minimize the amount of moisture entering the sheet flutes.
Please click here for Multiwall Polycarbonate & Condensation PDF